The manufacturing sector has consistently led the way in technical innovation, adapting to the needs of a global economy. The use of robotics in production lines has been one of the biggest developments in manufacturing in recent years. In addition to changing the way goods are manufactured, robotics has completely reinvented what manufacturing is all about, which has improved productivity, accuracy, and adaptability. This blog will examine the major advantages, difficulties, and emerging trends of robotics as it revolutionizes production lines and manufacturing.
The Rise of Robotics in Manufacturing
Though not entirely new, the use of robotics in manufacturing has grown significantly during the last ten years. Robots can now complete increasingly complicated jobs faster and more accurately than they could have in the past because to developments in artificial intelligence (AI), machine learning, and sensor technologies. These days, robots are used in every stage of the production process, from electronics manufacturing to vehicle assembly lines.
Key Benefits of Robotics in Manufacturing
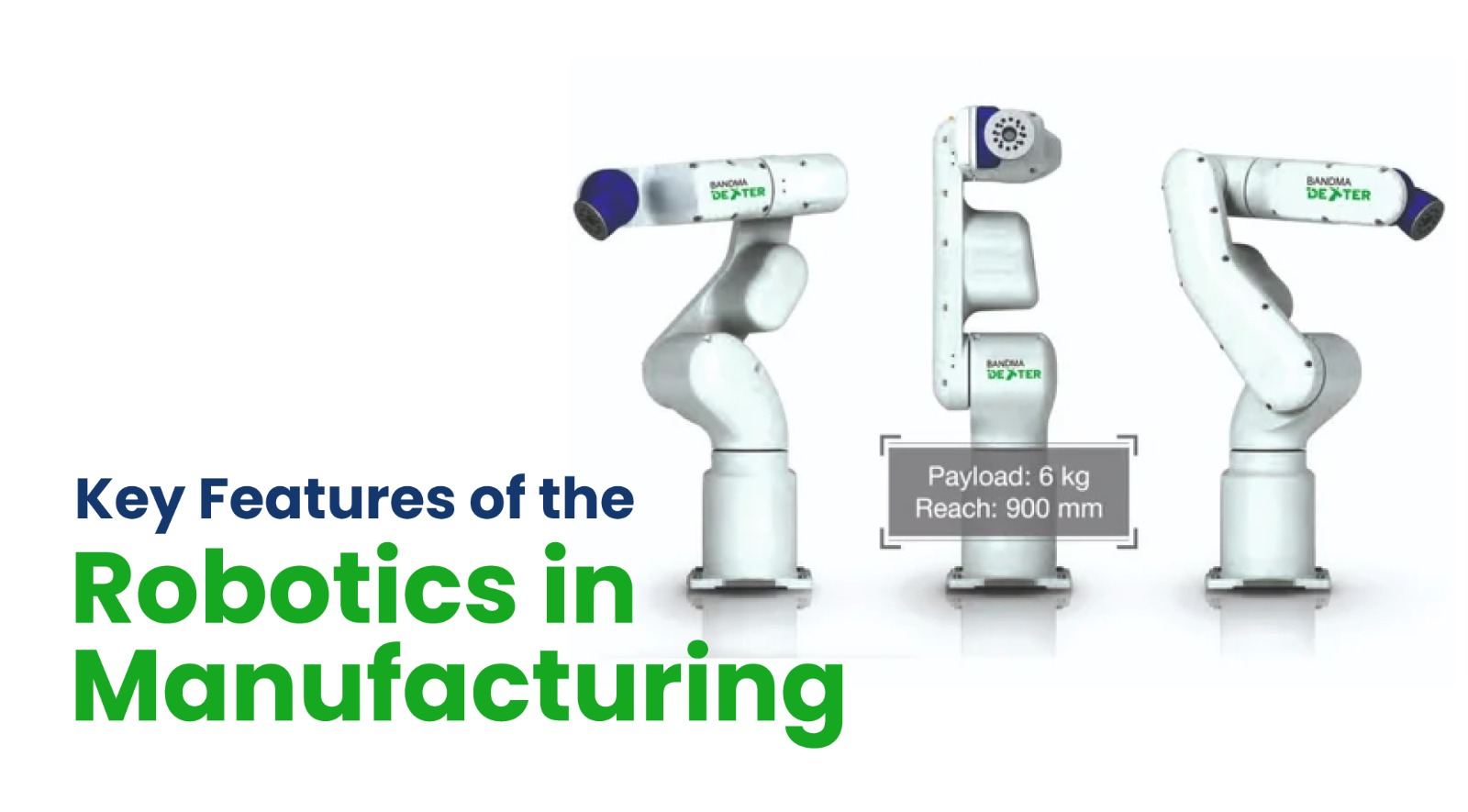
The integration of robotics into manufacturing and production lines offers numerous benefits that are driving its widespread adoption:
- Increased Efficiency and Productivity: Robots don't require breaks, sleep cycles, or shift work—they may operate continuously. Because of this constant operation, productivity rises significantly and manufacturers are better able to meet deadlines and high expectations. Robots can also complete repeated jobs at a steady pace, which shortens cycle times and boosts productivity all around.
- Enhanced Precision and Quality: Robotics has many benefits, one of which is its unmatched precision in task execution. Robots provide accuracy in areas like electronics and aerospace where even minor mistakes can result in large losses. They guarantee that items are assembled according to exact specifications, reducing faults and raising product quality.
- Improved Safety: Manufacturing settings can be dangerous, with potential dangers ranging from heavy machinery accidents to exposure to toxic compounds. Robots contribute to a safer workplace by automating physically taxing or risky tasks, hence lowering the risk of occupational injuries to humans. Robots can also function in hazardous areas with high temperatures or toxins where it would be dangerous for people to be present.
- Cost Reduction: The long-term cost savings from robotics outweigh the sometimes large initial expenditure. Robots eliminate waste by optimizing material utilization, decrease the requirement for manual labor, and decrease the possibility of errors that could result in expensive rework. These elements work together to reduce production costs over time, which boosts the profitability of manufacturing businesses.
- Flexibility and Adaptability: Reprogramming modern robots to perform multiple jobs with little downtime is possible due to their great degree of adaptability. Businesses where product lines are constantly changing or where customization is essential will find great value in this flexibility. Robots let producers respond faster to changing market conditions and client demands by swiftly learning how to do new activities.
Applications of Robotics in Manufacturing
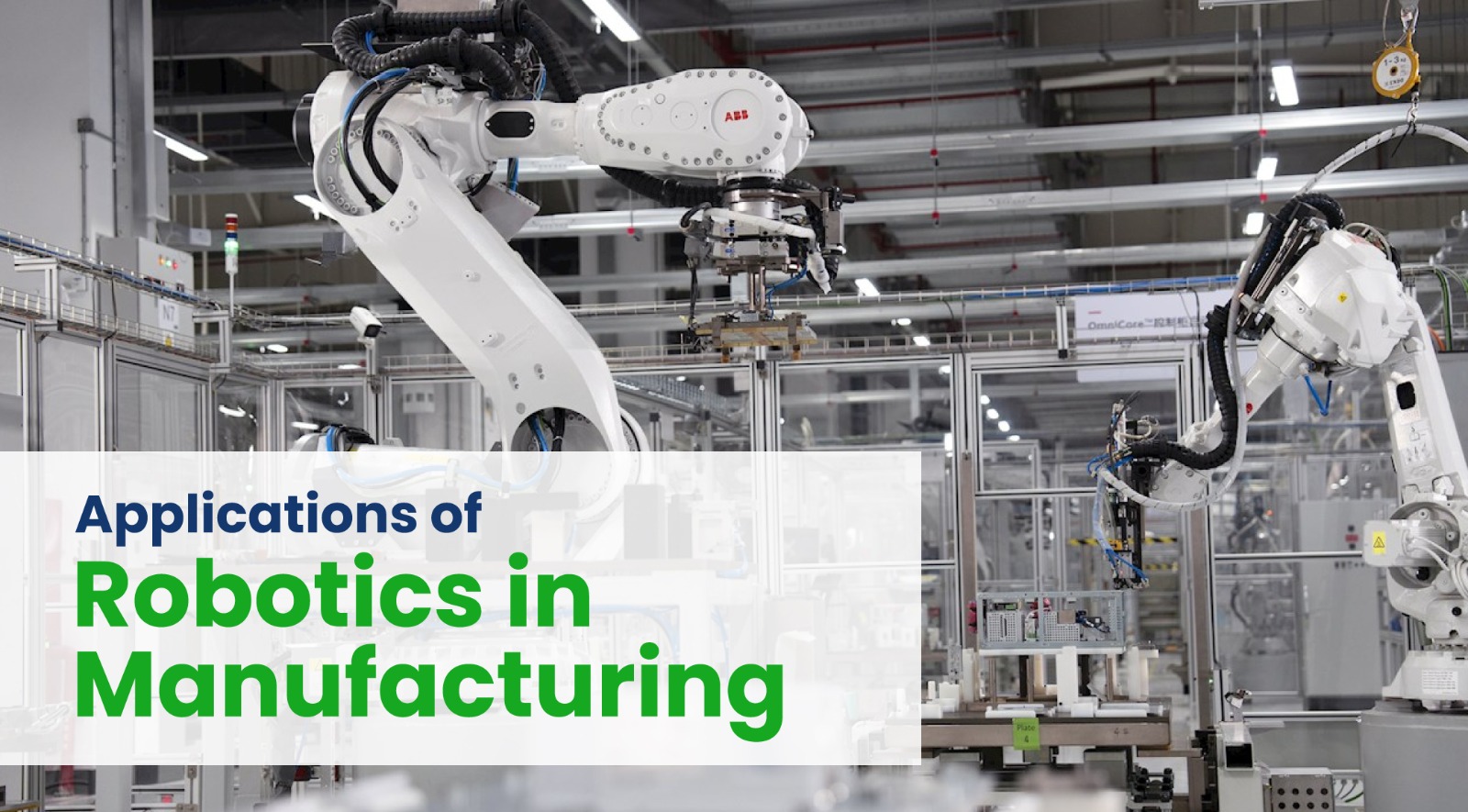
Robotics is being applied across a wide range of manufacturing sectors, each with its unique requirements and challenges. Here are some of the key applications:
- Automotive Industry: Robots are being utilized for jobs including welding, painting, assembling, and quality control in the automobile industry, which has been a leader in this field. Robots' accuracy and reliability guarantee that cars are put together to the highest standards while cutting production times.
- Electronics Manufacturing: Robots are essential in the electronics industry because they perform activities like PCB assembly, soldering, and testing, where components are frequently small and delicate. Robots' precision in handling small parts lowers the possibility of harm and guarantees that electronic equipment operates as intended.
- Food and Beverage Industry: Palletizing, quality control, and packaging are three tasks that robotics is utilized for in the food and beverage sector. Robots speed up the packaging process to accommodate increasing customer demand while simultaneously avoiding human touch with food goods, helping to maintain cleanliness requirements.
- Pharmaceuticals: Robots are employed in the pharmaceutical industry to perform functions like labeling, filling, and examining medications. Robots' accuracy and reliability guarantee that pharmaceuticals are manufactured in accordance with strict regulatory requirements, lowering the possibility of contamination and guaranteeing patient safety.
- Metalworking: Robots are used in metalworking to perform operations like material handling, welding, and cutting. In this industry, robotics is used to increase accuracy and consistency, decrease wasteful material use, and guarantee that metal components fit precise standards.
Challenges of Implementing Robotics in Manufacturing
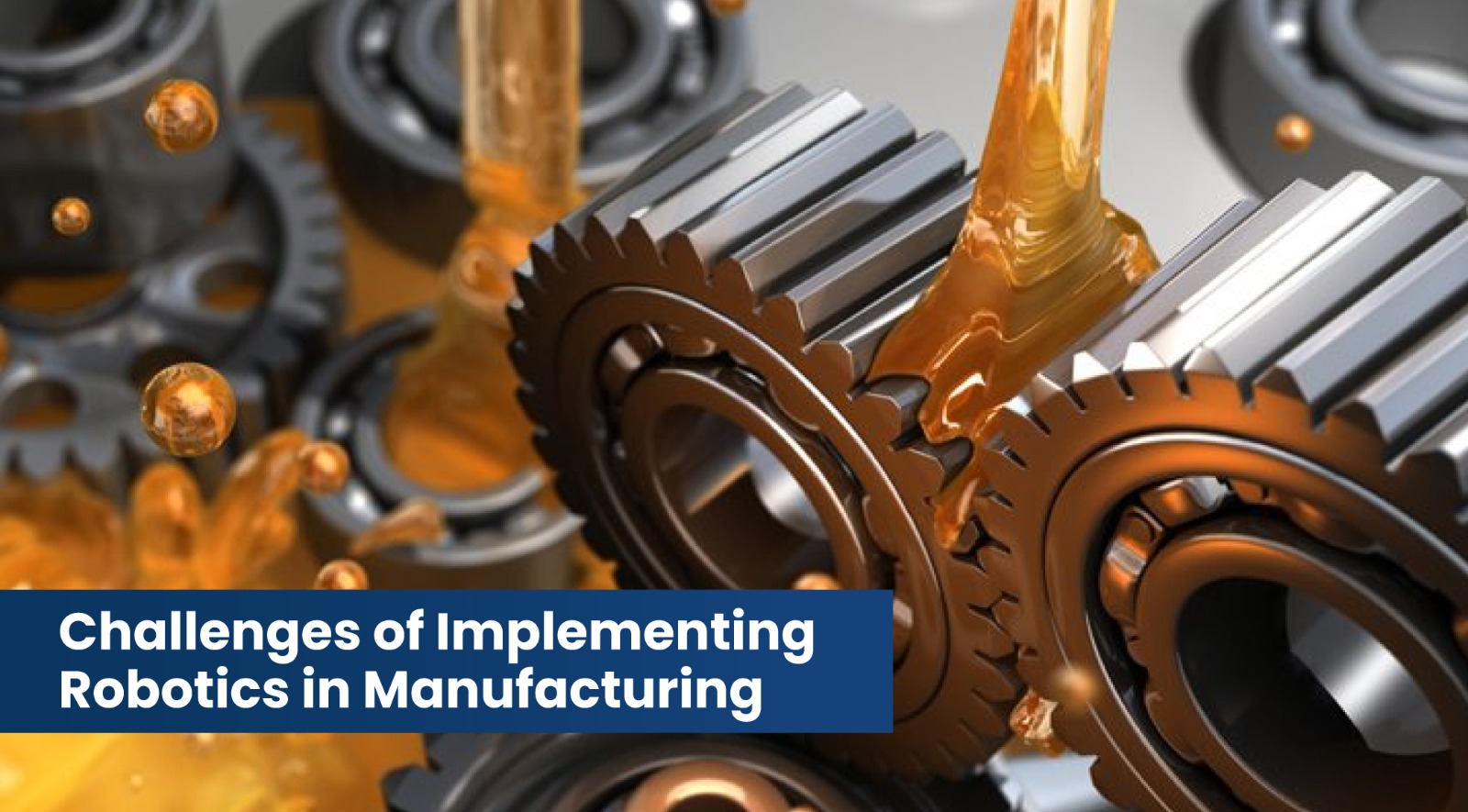
Despite the many advantages, the integration of robotics into manufacturing is not without its challenges. These challenges must be addressed to fully realize the potential of robotics in the industry:
- High Initial Costs: Robotic systems can be prohibitively expensive initially, especially for small and medium-sized businesses (SMEs). The expenses associated with buying, deploying, and maintaining robots, as well as teaching employees how to use them, can add up. Many manufacturers do discover, nevertheless, that the long-term advantages outweigh the upfront expenses.
- Skill Gaps: There is an increasing need for personnel with the expertise to operate, program, and maintain these systems as robots become more common in production. Adoption may be hampered by the lack of competent workers in the automation and robotics fields. If manufacturers want to develop a workforce that can operate alongside robots, they need to invest in education and training.
- Integration with Existing Systems: It can be difficult to integrate robots into production lines that are already in place, especially in older facilities where the infrastructure could not support contemporary robotic systems. In order to avoid disturbances and guarantee that robots can function flawlessly with current equipment, manufacturers must meticulously arrange the integration procedure.
- Cybersecurity Risks: Robots are more susceptible to cybersecurity risks as they are incorporated into digital networks and grow more linked. Strong security measures must be put in place by manufacturers to guard against cyberattacks that could halt production or jeopardize important data on robotic systems.
- Resistance to Change: Workers who are concerned about losing their jobs may oppose the introduction of robotics. In order to rectify this, manufacturers need to inform workers about the advantages of robotics, such the development of new, highly trained positions, and involve them in the transition process.
The Future of Robotics in Manufacturing
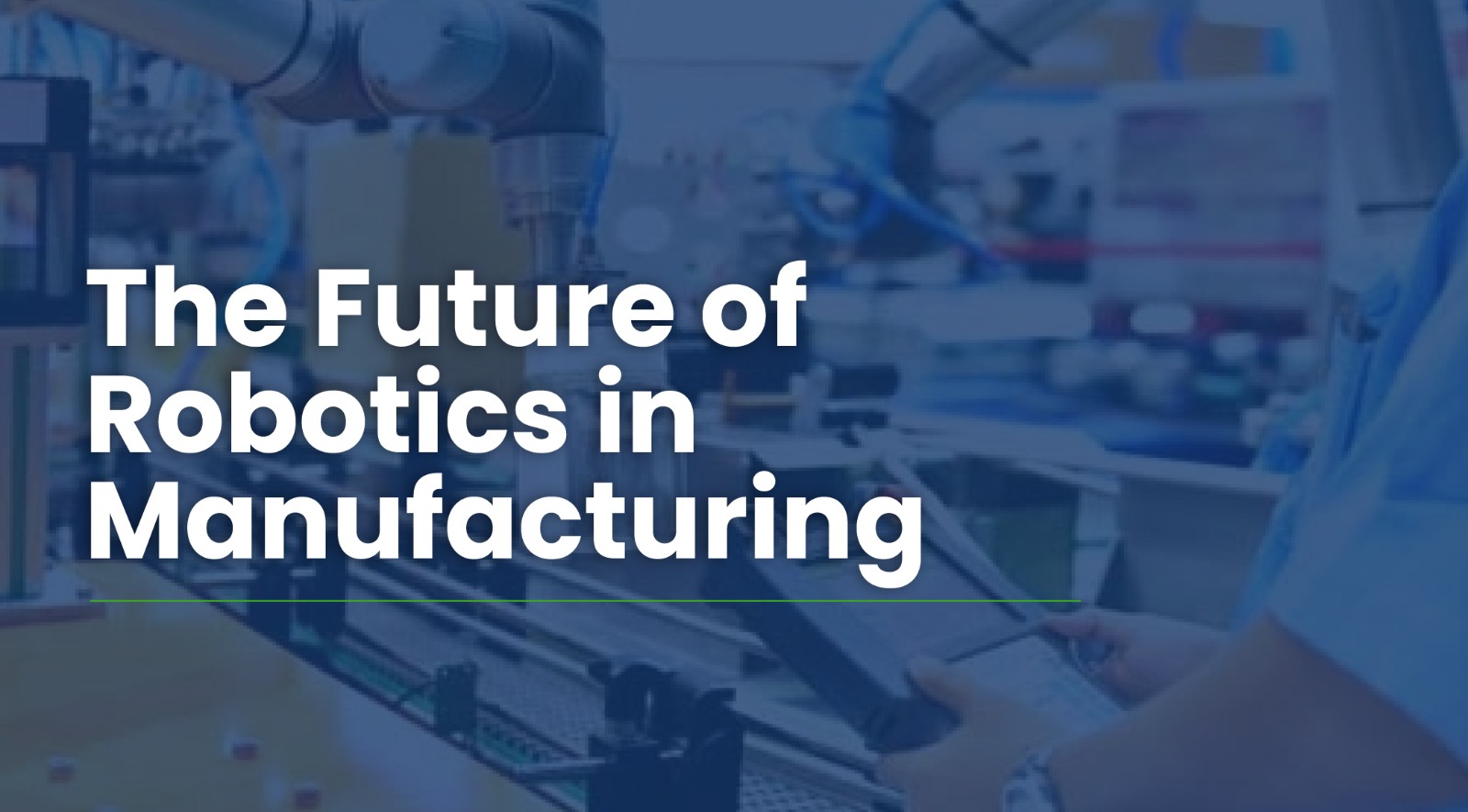
The future of robotics in manufacturing is bright, with continued advancements in technology set to drive further innovation. Here are some trends to watch:
- Collaborative Robots (Cobots):Cobots are made to work alongside humans, boosting productivity and complementing their talents. Cobots are perfect for activities that call for a combination of human skill and robotic precision because they can operate securely in close proximity to humans, unlike traditional robots, which are frequently housed in cages for safety.
- AI and Machine Learning:Robots are becoming more intelligent and self-sufficient thanks to the use of AI and machine learning. These innovations further augment the capabilities of robots by enabling them to learn from mistakes, adjust to novel tasks, and make judgments instantly.
- 3D Printing and Additive Manufacturing:The development of additive manufacturing, or 3D printing, is largely due to robotics. Robots automate the printing process, increasing accuracy and speed while making it possible to produce intricate, bespoke parts.
- Advanced Sensors and Vision Systems: Robots are becoming more accurate and versatile in their job performance because to the advancement of sophisticated sensors and vision systems. Robots can now "see" and understand their surroundings thanks to these technologies, which increases their adaptability to various jobs and industrial settings.
- Sustainability and Energy Efficiency: Robotics will be crucial in cutting energy use and waste as the manufacturing sector becomes more environmentally conscious. Robots can streamline production procedures to use less material, use less energy, and promote environmentally friendly manufacturing methods.
Conclusion
Production lines and manufacturing are being revolutionized by robotics, which has many advantages including improved accuracy, safety, adaptability, and efficiency. The long-term benefits of robotics integration outweigh the obstacles it poses. The use of robotics in manufacturing will only increase as technology develops, spurring additional innovation and changing the sector.
Manufacturers who adopt robotics will have an advantage in meeting customer expectations, competing in the global market, and achieving sustainable growth. Businesses can make sure they are prepared for the manufacturing of the future by investing in robotics today.