Packaging techniques need to be dependable and efficient in businesses where it's important to secure big loads. For enterprises managing heavy-duty applications, bandstrapping—a reliable technique of product security during transportation—has become essential. Unmatched strength and durability are provided by this technique, which is made possible by bandstrap machines and is a vital instrument in many industrial industries. These blog posts will discuss the main advantages of employing bandstrap machines in heavy-duty applications and how they improve cost-effectiveness, efficiency, and safety.
1. Superior Load Security
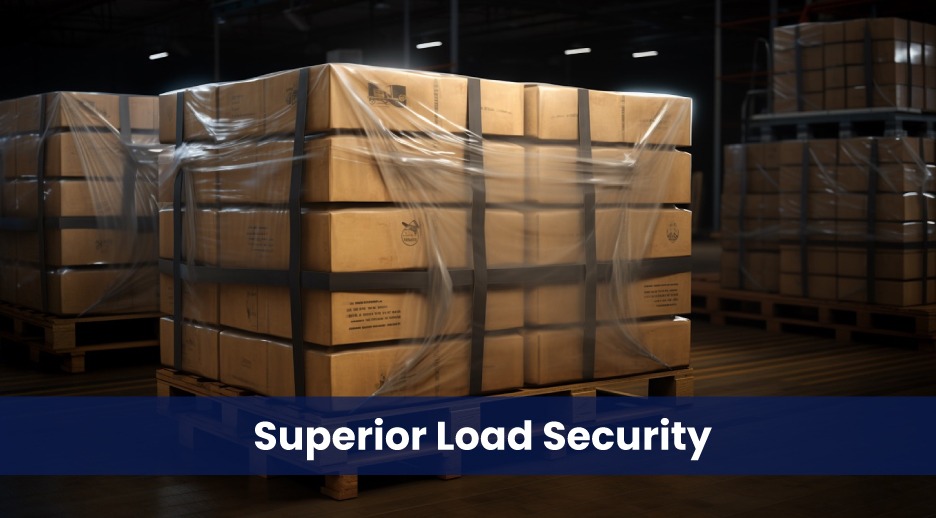
The capacity of bandstrap machines to securely and effectively secure weights is one of the main advantages of employing them in heavy-duty applications. Bulky or irregularly shaped products are frequently used in heavy-duty applications; to prevent movement during transit, these products need to be packaged in a stable and secure manner. By securing goods firmly together, bandstrapping lowers the possibility that they will move, topple over, or sustain damage while in transit.
The strapping material can be securely fastened without causing damage to the load thanks to the high precision with which bandstrap machines can apply tension. For instance, high tension levels can be used with polyester or steel strapping to guarantee that even the heaviest loads don't come undone during handling or transit.
2. Increased Efficiency in Packaging
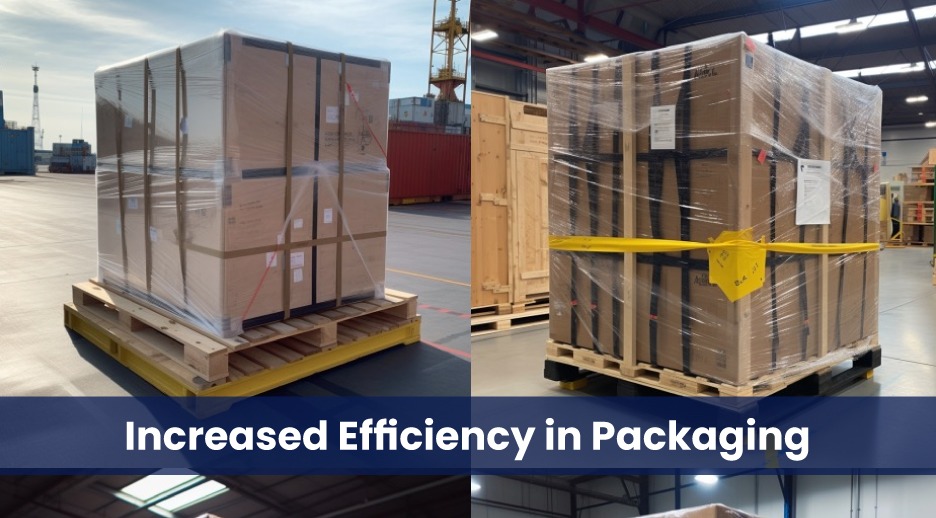
Packaging activities may be completed much more quickly and efficiently thanks to the automation of the strapping process provided by bandstrap machines. Time is a crucial component in industries that handle big amounts of merchandise. In addition to taking longer, manual strapping results in inconsistent load security since there is variation in the tension applied to the straps.
The procedure becomes more rapid, consistent, and dependable with bandstrap machines. These devices can apply strapping consistently and at a uniform tension, reducing human error and increasing output. Heavy-duty applications where big objects like steel coils, wood, bricks, or massive machinery need to be strapped on a regular basis will benefit most from this.
Furthermore, it is possible to include automated bandstrap machines into already-existing production lines, enabling smooth and continuous packing procedures. By preventing strapping from becoming a process bottleneck, this integration eventually improves overall operational efficiency.
3. Durability and Strength of Bandstrapping Materials
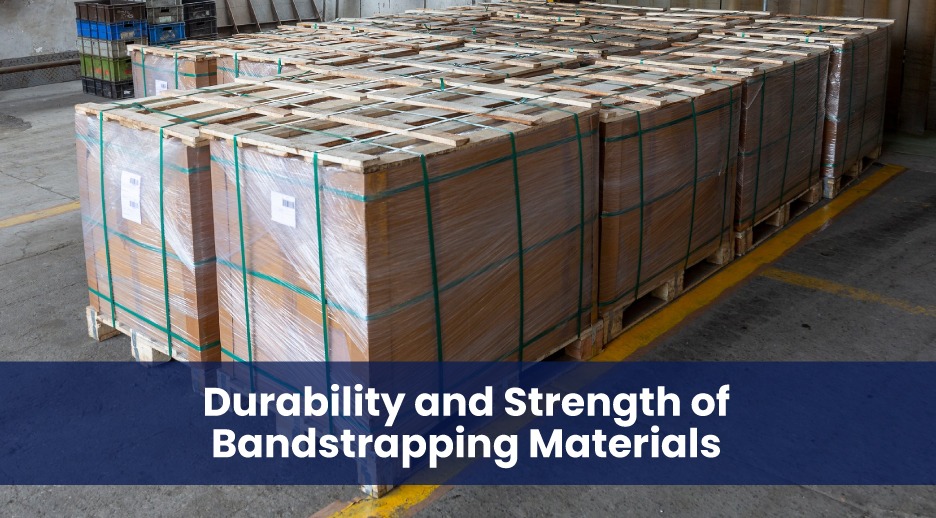
Bandstrapping materials, such steel, polyester (PET), and polypropylene (PP), are very strong and durable, which makes them perfect for heavy-duty applications. Various materials offer different benefits based on the type of load.
- Steel Strapping: Steel strapping, which has a high tensile strength, is perfect for securing bulky, heavy objects like concrete blocks, steel beams, and other building supplies. Because of its maximum holding power and resistance to extreme temperatures, it makes sure that the load is secure even in challenging circumstances.
- Polyester (PET) Strapping: Because of its great strength, flexibility, and endurance under tension over time, PET is a well-liked substitute for steel. It works well with loads that can expand or compress, such plastic, paper, and wood items. PET strapping is perfect for outdoor storage or transit since it resists corrosion.
- Polypropylene (PP) Strapping: For lighter, heavier loads, PP is an affordable choice. It is commonly utilized in situations where flexibility and price are crucial, although not being as robust as PET or steel. PP strapping is frequently used in consumer goods, food product, and lighter industrial material packaging.
These materials lower the possibility of damage during storage or transit by ensuring that even the largest loads are safely secured and shielded.
4. Enhanced Safety for Workers
In any industrial setting, worker safety is of utmost importance. In the packing process, bandstrap machines are essential for enhancing workplace safety. Workers may be at risk when manually strapping, particularly when using sturdy materials like steel. Physical strain and wounds from the tensioning process are possible side effects of hand strapping.
However, these procedures are automated using bandstrap machines, which lowers the danger of harm and eliminates the need for manual labor. The automatic tension control feature on these machines guarantees that the proper force is given to the straps without putting personnel in risk. Workplace safety can be further improved by fully automated systems, which in certain situations can do away with the need for human intervention completely.
Furthermore, automatic bandstrapping lowers the danger of strain-related accidents by eliminating the need for employees to frequently carry or move large loads.
5. Cost Savings Over Time
Although a bandstrap machine may seem like a big initial expenditure, it can save a lot of money over time. Labor expenses are decreased by automation in the strapping process since fewer workers are required to complete manual strapping. Machine-applied strapping's consistency and speed increase throughput, enabling companies to package and ship more goods in less time.
Savings on materials is also facilitated by bandstrap machines. When strapping is done manually, workers may apply more strapping than is necessary to secure a load, which frequently results in the abuse of strapping materials. However, because bandstrap machines only apply the necessary quantity of strapping at the right tension, they use resources more efficiently. Over time, this decreases the cost of consumables and minimizes waste.
Additionally, bandstrap machines save organizations money by avoiding product damage during transit and the accompanying costs of returns, replacements, and repairs. Loads that are securely strapped are less likely to move, tumble, or sustain damage during handling or transit, guaranteeing that the goods arrive at their destination undamaged.
Conclusion
The advantages of employing bandstrap machines in heavy-duty applications are evident, particularly when dealing with huge, heavy, and frequently irregularly shaped items. For companies managing high-demand packaging requirements, bandstrap machines are a vital asset, offering greater load security as well as improving worker safety and operating efficiency.
Even the most demanding weights are successfully secured thanks to the strength and durability of bandstrapping materials like PET and steel, which reduces the possibility of damage occurring during transit. Additionally, bandstrap machines are a wise investment for companies trying to enhance their packaging processes because to the long-term cost benefits linked to automation and material efficiency.
Adopting bandstrap machines is not only a convenient solution for heavy-duty firms; it's a calculated decision that can increase profitability, production, and safety.