Have you ever wondered how goods are kept safe in transit? Why do some shipments look to have weathered a storm, while others arrive in perfect condition? Effective packaging is key, and the stretch wrapper is one of the unsung heroes of the packaging industry.
Stretch wraps are essential for making sure items are packaged securely and lowering the possibility of damage occurring while in transportation. These devices, which offer efficiency, cost savings, and improved product protection, have completely changed the packaging sector. It's crucial to comprehend stretch wrappers if you ship or store things for a living. Explore this guide to learn all there is to know about stretch wraps and make sure your goods always arrive at their destination in excellent shape.
What is a Stretch Wrapper?

Having worked for a considerable amount of time in the packaging sector, I have seen firsthand how revolutionary stretch wraps can be. These devices are revolutionaries in their field, not only tools. The basic purpose of a stretch wrapper is to encircle objects with stretchable plastic film, mostly to maintain their stability and bundling while storage or transit.
Brief history and evolution of stretch wrappers
Stretch wrappers were first developed in the latter half of the 20th century. The necessity for effective packaging solutions increased as businesses expanded, and creative thinkers started creating devices that could automate the wrapping process. The foundation for the complex, automated devices we see today was built by the primitive, frequently manual early models. As I've developed my knowledge and skills over the years, I've watched these machines change—becoming more effective, user-friendly, and flexible to meet different packaging requirements
Types of Stretch Wrappers
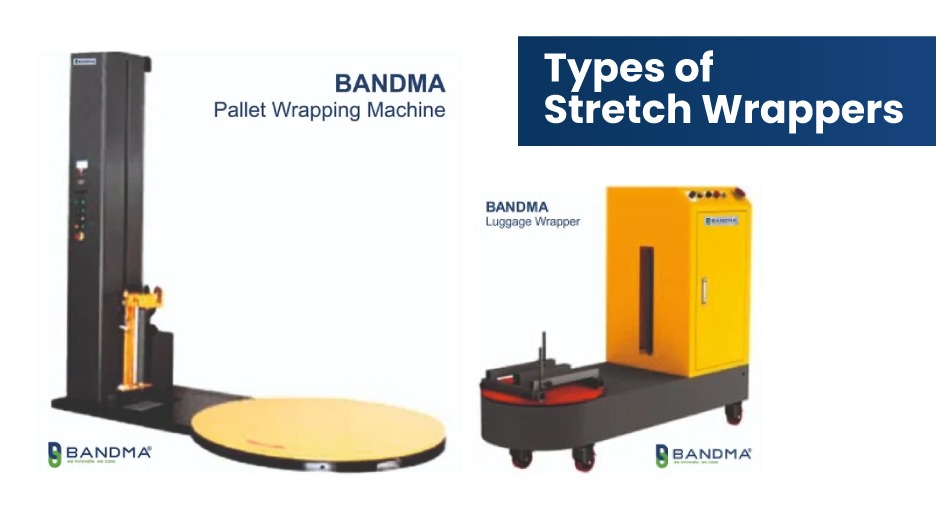
Bandma considering the diversity offered, it might be a little confusing to navigate the world of stretch wrappers. I'm here to offer my expertise of the subtleties of each type that I've had the honor of working with over the years.
1. Turntable Stretch Wrappers
These are perhaps the most prevalent kind in small- to medium-sized businesses that I have come across. The product is set on a revolving platform, and the film is wrapped around it while it rotates. It's a simple method that works amazingly well for many different kinds of things.
2. Rotary Arm Stretch Wrappers
These work best, in my opinion, for bigger or more unsteady loads. To apply the film, the machine's arm revolves around the product rather than the product itself. It guarantees that the product maintains its stability while receiving a tight wrap.
Key Components of a Stretch Wrapper
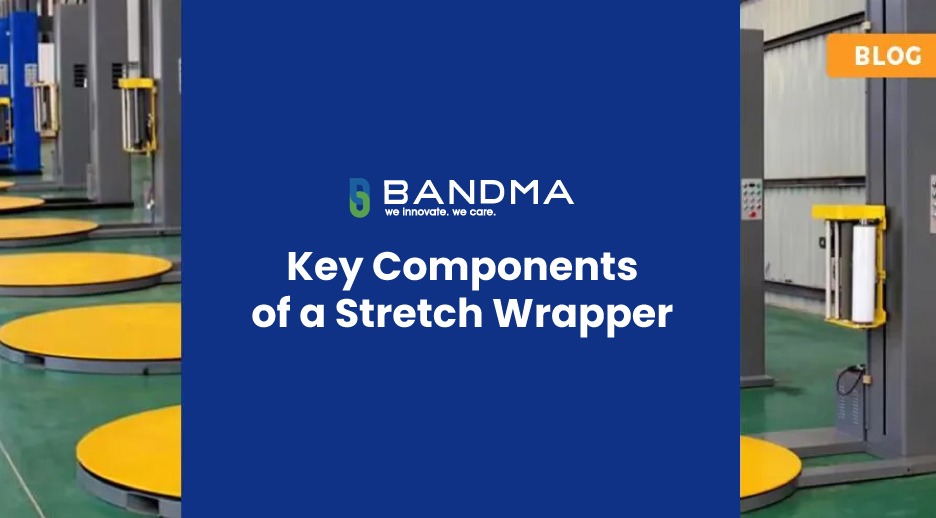
Film Delivery System:
The stretch wrapper's core is this. The film is applied, stretched, then dispensed to the product. The quality of the wrap is determined by how precisely this method works. I have direct experience with the transformative power of a well maintained film distribution system when it comes to guaranteeing a product is wrapped safely.
Load Handling System:
The location of this component is crucial. It guarantees that the product is properly positioned and supported while being wrapped. The load-handling system is essential to any conveyor system or revolving table.
Control System:
Consider this to be the machine's brain. It enables users to adjust settings, manage processes, and guarantee the computer performs at its best. I've watched control systems change over the years, going from simple manual installations to complex digital interfaces.
Benefits of Using Stretch Wrappers
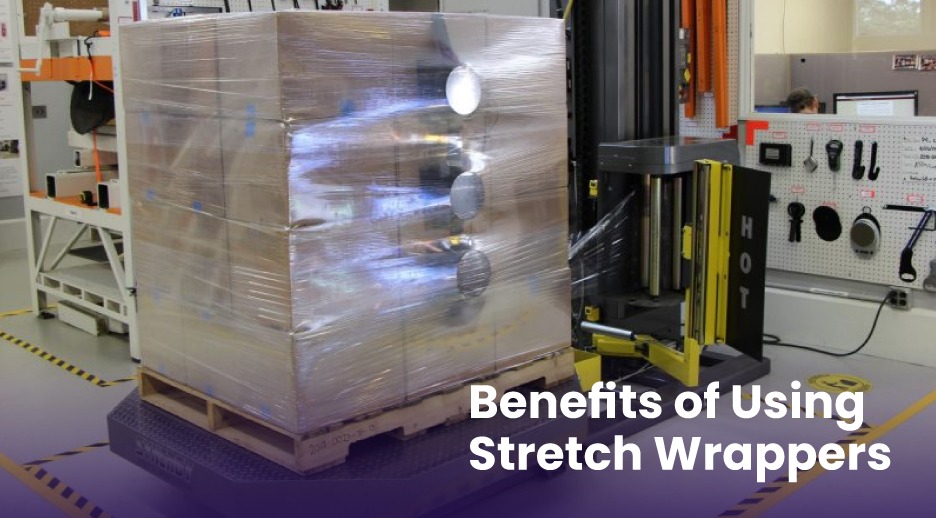
Throughout my career in packaging, I've been asked a lot of questions concerning the real advantages of employing stretch wraps. Based on my vast expertise, I can declare with confidence that these devices have several benefits beyond product wrapping. Let's examine a few of the most notable advantages.
1. Improved Packaging Efficiency
When I started working with stretch wrappers, their sheer speed and consistency were among the first things I noticed. Faster product wrapping and consistent wrapping—which is difficult to accomplish by hand—are the results.
2. Enhanced Load Stability
I can attest to the steadiness of a well-wrapped load because I have witnessed innumerable shipments being ready for shipment. Stretch wrappers reduce the possibility of product moving during transportation by ensuring that the products are snugly packaged.
3. Cost Savings
Eventually, the savings mount up. Businesses can experience a considerable reduction in packaging expenses with less film wasted and faster wrapping times. It's a self-sustaining investment.
4. Reduced Product Damage
A product is protected if it is well-wrapped. Because stretch wrappers offer a protective covering, I've seen a decrease in returns and complaints for broken goods.
5. Eco-friendly Advantages
Nowadays, sustainability is critical. Because many companies choose recyclable films and modern stretch wrappers are made to utilize less film, the overall process is more environmentally friendly.
Stretch wrappers are a commitment to quality, sustainability, and economy when they are used in your packaging process. It's not only an efficiency move. You'll benefit from having faith in the process.
Maintenance and Safety Tips
It is crucial to make sure your stretch wrapper operates safely and for a long time. I've accumulated some crucial maintenance and safety advice over the years from working in the field, which can have a big impact on both the machine's performance and the workers' safety.
Regular Inspection and Cleaning:
Stretch wrappers gather dust and particles with time, just like any other machinery. Regular inspections can assist in spotting wear and tear and guarantee prompt replacements or repairs. Maintaining cleanliness, particularly in the film distribution system, guarantees error-free performance and lowers the likelihood of problems.
Proper Training for Operators:
A safe operator is one who is well-informed. Make sure everyone has received thorough training before letting them operate the machine. This reduces the possibility of mishaps while simultaneously guaranteeing effective operation.
Safety Precautions and Best Practices:
Always follow the safety instructions provided by the manufacturer. This entails putting on safety gear, making sure the machine is off while doing maintenance, and clearing the workspace of any obstacles. When followed regularly, simple procedures can avoid accidents and guarantee a secure workplace.
Conclusion
Over the course of my years navigating the packaging market, stretch wrappers have become incredibly important. These devices serve as pillars, minimizing damage, guaranteeing that goods are wrapped securely, and maximizing operational effectiveness. It is impossible to overestimate their importance in today's sectors. I can't emphasize enough how important it is to invest in high-quality equipment since I have personally seen the transformative power of high-quality stretch wrapping solutions. It's a long-term commitment to quality, guaranteeing returns over time, and laying the groundwork for success.